In the field of modern precision manufacturing, five-axis machining centers have become key equipment in industries such as aerospace, automobile manufacturing, and mold processing due to their high efficiency, high precision, and complex shape processing capabilities. As a leading company in the field of machine tool manufacturing, NingQing focuses on the research and development and manufacturing of five-axis machining centers, and is committed to providing high-performance, high-stability intelligent processing equipment. This article will deeply analyze the core technical advantages of NingQing's five-axis machining center and its application in the field of high-end manufacturing.
1. Five-axis linkage technology to achieve high-precision complex processing
Traditional three-axis machine tools usually require multiple clamping and adjustments when processing complex parts, which is prone to cumulative errors. NingQing's five-axis machining center can complete the processing of multiple surfaces in one clamping through the linkage control of the X, Y, and Z linear axes and the A and C rotary axes, thereby improving accuracy and efficiency.
High rigidity design of the rotary axis: A high-precision rotary table is used to ensure the dynamic accuracy of the rotary axis and reduce errors caused by changes in cutting force.
Five-axis linkage algorithm optimization: NingQing adopts advanced interpolation calculation and error compensation technology to effectively reduce the trajectory error in surface processing and ensure high-precision processing effect.
2. High-speed and high-precision spindle system to meet stringent processing requirements
The spindle performance directly affects the processing quality and efficiency of the machine tool. NingQing five-axis machining center is equipped with a high-speed electric spindle, which can achieve high-speed cutting, improve processing efficiency, and ensure surface quality.
High-speed direct-drive electric spindle: The maximum speed can reach 24,000rpm, which is suitable for high-speed cutting of difficult-to-process materials such as aluminum alloy and titanium alloy.
Oil mist lubrication and cooling system: The high-precision spindle adopts oil-gas lubrication and water cooling system to effectively reduce spindle heating, improve stability and extend service life.
Online dynamic balancing detection: Automatically detect and adjust the dynamic balance of the spindle, reduce vibration and improve surface finish.
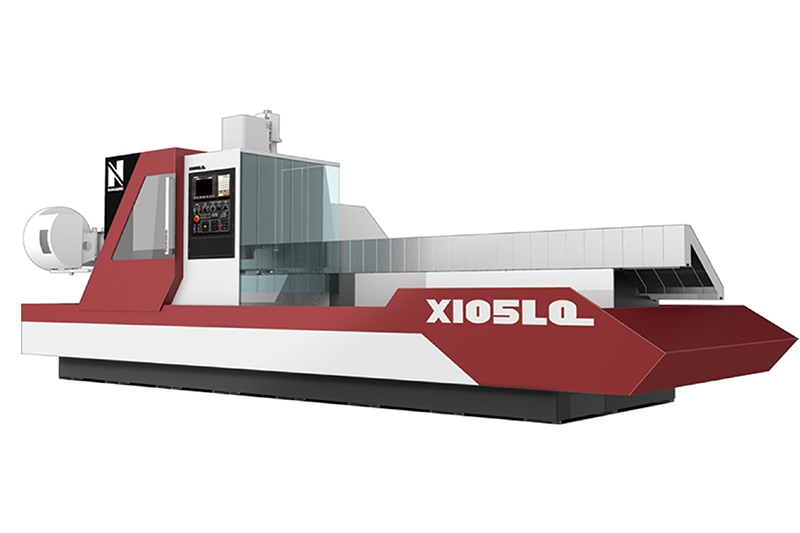
3. Advanced CNC control system, both intelligent and stable
The control system is the "brain" of the five-axis machining center, which determines the operation stability and intelligence of the machine tool. NingQing five-axis machining center adopts internationally advanced CNC control system, supports five-axis linkage and intelligent optimization, and ensures efficient and high-precision machining of complex parts.
Intelligent tool path optimization: automatically calculate the optimal tool path, reduce empty cutting, and improve machining efficiency.
Error compensation system: adopts laser interferometer and ballbar detection technology to automatically compensate for thermal deformation errors and improve machining accuracy.
Intelligent machining monitoring system: real-time monitoring of spindle load, cutting force and temperature, providing predictive maintenance, and reducing failure rate.
4. High-rigidity structure design to improve machining stability
During high-speed cutting, the five-axis machining center needs to maintain extremely high structural stability to ensure machining accuracy. NingQing machine tool adopts high-rigidity gantry frame design, and optimizes the machine tool structure through finite element analysis (FEA) to ensure long-term stable operation.
Integrated casting body: adopts high-strength cast iron to improve seismic resistance and thermal stability.
Ball screw and linear guide: imported high-precision ball screw and linear guide are selected to ensure high dynamic response and repeat positioning accuracy.
Active thermal compensation technology: Real-time monitoring of the temperature of key parts of the machine tool through temperature sensors, automatic adjustment compensation, and reducing the impact of thermal deformation on processing accuracy.
5. Wide application fields, helping high-end manufacturing
With high precision, high efficiency and intelligent control, NingQing five-axis machining center is widely used in the following fields:
Aerospace: Processing turbine blades, engine parts, fuselage structural parts to improve product consistency and quality.
Automobile manufacturing: Precision machining of engine cylinders, gearbox housings and complex molds to improve production efficiency.
Mold manufacturing: Suitable for high-precision machining of complex curved surface molds, stamping molds, and injection molds, reducing subsequent manual polishing.
Medical equipment: Production of high-precision medical parts such as artificial joints and dental implants.
Conclusion
NingQing five-axis machining center relies on core technologies such as five-axis linkage technology, high-speed spindle system, intelligent CNC control, and rigid structure design to help high-end manufacturing companies achieve efficient, precise and stable processing needs. In the future, with the development of intelligent manufacturing and Industry 4.0, NingQing will continue to optimize five-axis machining technology and provide more advanced machine tool solutions for the global manufacturing industry.